PCI-DMC-A01
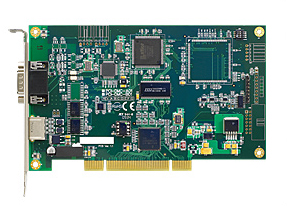
Application
Electronic components, printing machines, woodworking machines, discharge machines, adhesive machines, tube bending machines.
Specification
Supports Delta ASDA-A2-F series AC servo drives. 35 kinds of homing modes. T-curve / S-curve velocity profiles. Linear, circular and continuous interpolation supported. Supports VB, VC, BCB, DELPHI, C#, VB.NET tool languages. PCI Specifications Ver.2.2, supports 32-bit, 3.2V/5VDC operation. Complies with noise ordinances. Operating Temperature: 0oC~50oC; Storage Temperature: -20oC~70oC; Humidity: 5~95% (non-condensing).
FEATURES
High Integrated Capability
With DMCNET structure, multiple control devices such as servo motors, remote digital and analog modules, stepping motors, direct drive motors (DD motors), and linear motors can be easily and quickly connected.
Up to 20Mbps communication bandwidth is provided. Maximum distance of the communication is 30m (98.4ft.)
Synchronous Control
Simultaneous 3-axis linear interpolation, 2-axis arc interpolation, 3-axis helical interpolation and continuous interpolation can be implemented. DMCNET is a motion control communication network which is able to update data every 1ms and offer the ability to control 12 servo system units or 4 groups, 3-axis interpolation algorithms synchronously. It is also capable of transferring the data of 12 servo motor units, or 768 digital inputs and outputs within 1ms simultaneously.
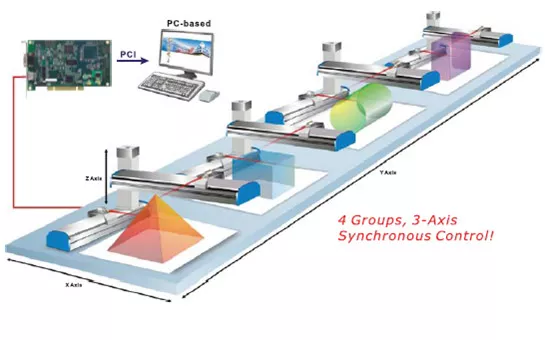
Description
Delta High-Speed Motion Control System is a high speed and real time communication system, capable of controlling up to 12 servo system units within 1ms simultaneously. It can accept double precision floating point values 64-bits wide and provide up to 1,280,000 pulse/rev resolution so the servo system can make accurate calculations and provide operation flexibility. 35 homing modes are provided. 12 servo system units or 4 groups, 3-axis helical and linear interpolation or 6 groups, 2-axis linear and arc interpolation can be implemented synchronously. It also supports absolute commands, incremental commands and T-curve / S-curve velocity profiles, built-in position, speed and torque control modes for different uses. Simply by connecting to servo motors, linear motors, digital inputs and outputs (DI/DO), analog inputs and outputs (AI/AO) and other control devices such as stepping motors and manual pulse generator (MPG), enabling fast and cost-effective communication and control is easy. is the best integrated platform for multi-axis and synchronous motion control in a wide range of machine tools and industrial applications. It is also the ultimate solution that provides effortless wiring, enhanced stability, flexible extension ability and versatile operation for industry upgrading and adding value to the products.
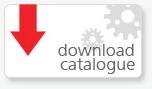